切削加工で精度を高めたい
- 複雑な形状を厳密な寸法で作りたい…
- 精密機器の動作を安定させたい…
- 微細な医療機器部品が必要…
- 製品性能を向上させたい…
- 今あるパーツを最適な形状にしたい…
F・Sが誇る「切削技術と経験を結集した高精度加工」
半導体製造が求める高精度に対応
半導体の製造装置内で使用されるシャフトを、
微細な寸法精度を維持して製作しました。
STORY
「PEEK製シャフトで樹脂切削の限界精度に挑む」
半導体製造の工程は多数あるが、露光プロセスはパターンを作る重要なステップだ。適切な露光量の維持、マスクの正確性、微粒子まで排除したクリーンな環境などを繊細に管理する必要がある。そんな半導体デバイス製造に先端技術を導入している企業から、F・S・エンジニアリングに極めて微細な樹脂部品の切削加工の依頼が舞い込んできた。それまでにも部品の製造実績がある既存顧客ではあったが、F・S・エンジニアリングの製品クオリティを信頼し、新たな依頼案件として重要なプロジェクトを提案してきたのだ。それが、半導体製造装置において露光プロセスで使用される樹脂製シャフトの製造だった。求められた寸法精度は樹脂材では高難度の±0.03。厳密さが求められる部品の製作を通じて、専門のエンジニアが樹脂の精度の限界に挑戦した。
半導体プロセスに適応する高性能樹脂
製作を依頼されたシャフトは、半導体製造工程でも特に精密な機構に重要な役割を果たす。リソグラフィ装置(微細な回路パターンを、紫外線などの放射で露光する装置)では、シャフトがマスクやウエハーの位置調整を担当する。求められたのは、微細な回転や移動を可能にすることだった。 そのための公差±0.03を実現する素材は、ポリエーテルエーテルケトン(PEEK)が選ばれた。PEEKはスーパーエンプラとして最高性能を持ち、抜群の機械的強度と耐久性を備える。また、高い耐熱性と低い摩擦係数を有し、プロセス中の高温環境や微細な動きにおける信頼性が高く、詳細な露光パターンを作り出すために最適な素材だった。
加工精度と切削計画の確立
PEEK製シャフトの切削加工を前に、エンジニアは高精度に挑む技術的プロセスを冷静に検討した。まず、適切な工具と切削条件を選定し、樹脂の種類や硬さに応じた切削パラメータを設定した。これにより、切削時の熱や振動を最小限に抑え、寸法の安定性を確保する。次に、適切な固定とセットアップが欠かせない。正確な位置決めや固定装置の設計によって、加工中の変位を最小化し、公差のばらつきを抑える。また、適度なクランプ圧力を保ちつつ、材料への過度な応力を回避した。
工具の交換や定期的なメンテナンスも適切であることを確認。鋭い切削刃と正確な刃先の状態を保つことで、加工精度が向上し、公差の制御が容易になるのだ。最後に、樹脂の特性を理解し、熱収縮や変形の可能性を考慮した加工を計画した。PEEKは切粉が絡みやすい素材で、こまめに分散させる加工プロセスとケアが重要だった。さらに、必要に応じて冷却作業を行いつつ、適切な切削速度を調整することで、材料の特性に合わせた精密な加工を可能にした。
いよいよ実際の加工作業が始まった。加工はヤマザキマザック製の複合機「QUICK TURN NEXUS 200-2 MY」で行うことになった。フライスと旋削の切削加工を効率的に進める、12本の工具を装備した複合機だ。外径と長さの切削、内径形状や溝の加工など、厳密な寸法公差が設定される箇所をまさに樹脂加工の技術と経験を集結して慎重に行った。
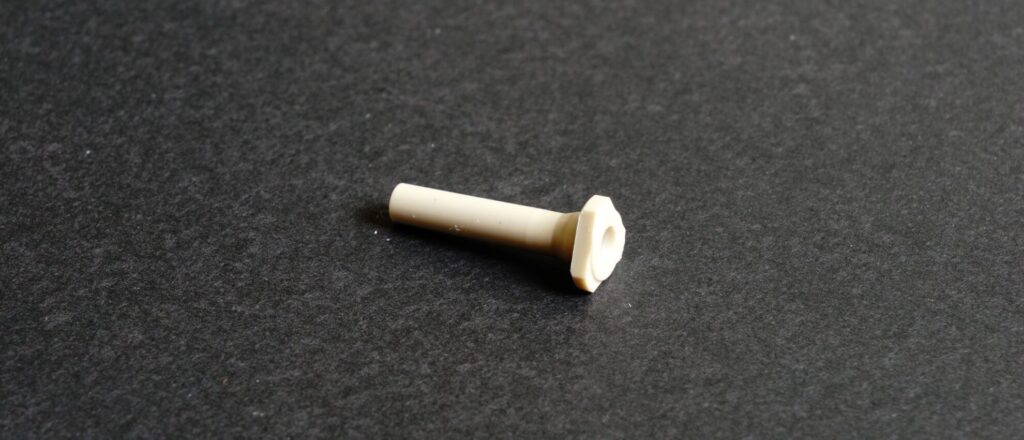
このシャフトの寸法精度は非常に厳しく、微小な位置のずれが半導体チップの製造に悪影響を及ぼす可能性があった。±0.03。樹脂切削ではかなり高い精度が要求された。だが、F・S・エンジニアリングのエンジニア達は諦めてはいなかった。「何としても、要求精度をクリアしてみせる」。そんなフロンティア精神に溢れていた。PEEKの持つスペックは、半導体製造工程が求める厳しい工学的要件をクリアしている。そして、これまでPEEK樹脂を多く切削してきた技術力と経験値が私たちにはある。そうして出来上がったPEEK製シャフトは、非常に微細だが、顧客の要求と切削加工業者のプライドを同時に満たす大きな成果となっていた。
確かな切削技術の証明
最終的に高品質な製品が完成し、予定どおりPEEK製シャフトは納品された。顧客は厳格な検査プロセスを経て、公差±0.03の高い精度を確認した。使用感も問題なく、プロジェクトは満足のいく結果が得られた。PEEK製シャフトの採用により、半導体製造プロセスの信頼性が向上し、微細な構造の半導体製造においても寸法安定性を確保することに成功した。一方、F・S・エンジニアリングは、外径・内径・溝のいずれも寸法公差内に収めた会心の出来に、自社の切削技術の高さを改めて証明することができた。また素材としてPEEKを採用したことで、この樹脂材であれば寸法精度や機械的性質を重視するアプリケーションにおいて、高品質な切削加工が可能であることを示したのだ。
樹脂製品の精度向上は製品の品質、持続可能性、競争力の向上を実現するためには追求し続けるべき至上命題だ。FSエンジニアリングは、エンジニアだろうが営業だろうが常に挑戦する意識を持ち、寸法精度に挑み続けていくだろう。
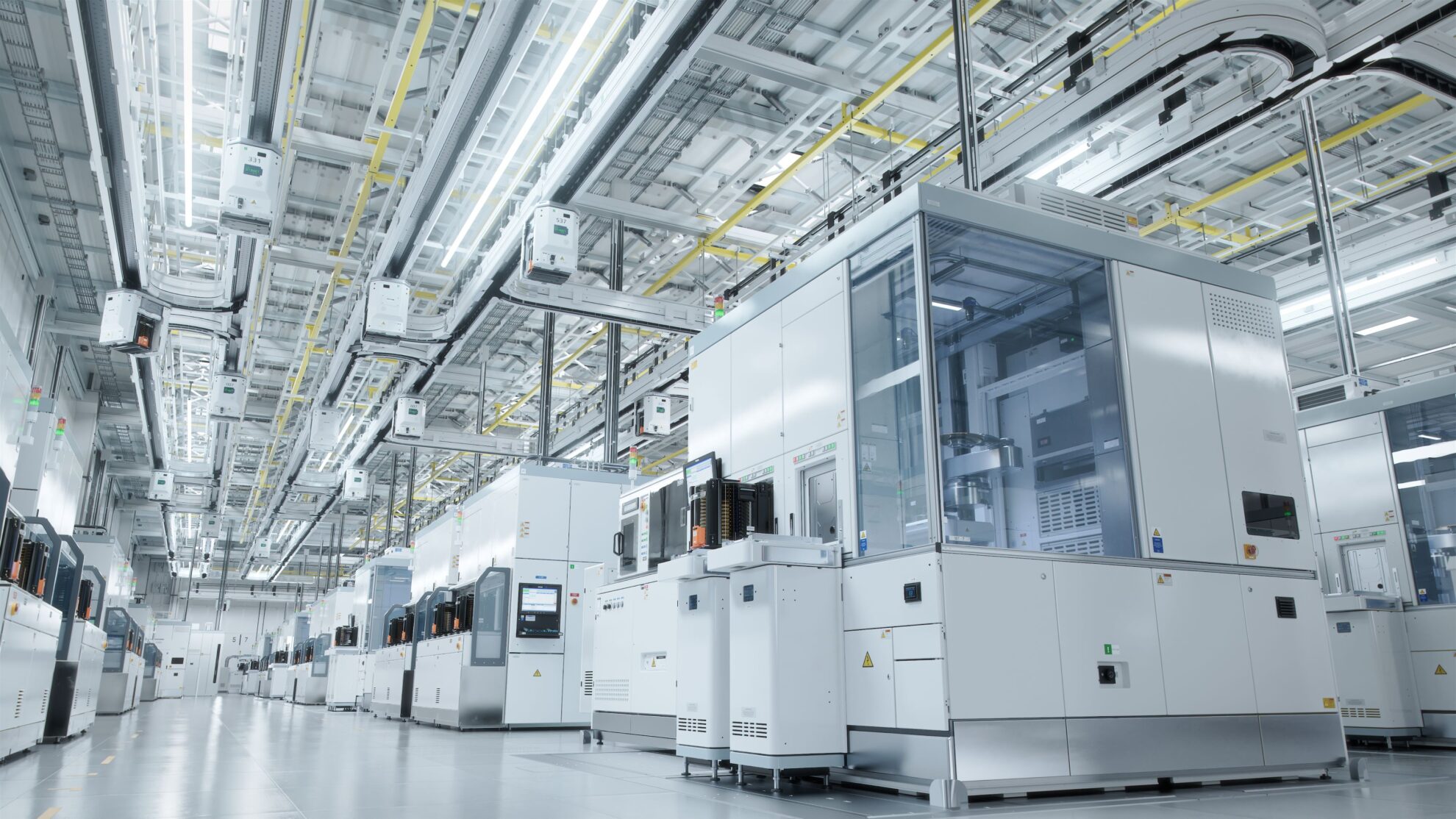
理想の製品は、一貫したクオリティで安定使用が確保され、経済効率を向上させるものだと考える。そんな製品を作り出せたら、社会貢献という意味でもエンジニア冥利に尽きる。精度の向上は、先進技術や革新的な設計の実現に寄与し、理想の製品にたどり着くための“進化”を促進させるのだ。
精度の向上は、先進技術や革新的な設計の実現に寄与し、理想の製品にたどり着くための“進化”を促進させるのだ。
高精度切削品の一例
たとえばこのようなパーツを製造致しました。
精密機器 装置内部品
- 電子部品製造の試験装置パーツ
- PEEK
- 22mm×25mm×7.5mm
POINT
- 精密機器を傷つけない為に樹脂部品を使用。
- 部品全体に高精度・高精密さを求められ、寸法安定性のある素材を採用。
- 削る面積が多く、反りやバリを極力抑えて加工。
精密機械 試験装置
- 電子機器の試験装置 樹脂部品
- PEEK
- 9mm×6mm×1.7mm
POINT
- 電子機器の精密部品に使用される樹脂パーツ。
- 寸法安定性に優れた高性能樹脂であるPEEKを採用。
- 微細な部品で、6カ所加工されている穴径はわずか0.1mm。