素材や加工方法を見直したい
- 既存パーツの性能に不満がある…
- 部品製作の費用・コストを抑えたい…
- パーツの軽量化を実現したい…
- 金属から樹脂に素材変更を検討したい…
- パーツを最適な形状に追加工したい…
F・Sが実践した「素材変更による性能と費用の最適化」
車載半導体部品の製造工程を最適化
高性能が条件となる車載半導体の製造パーツを金属から樹脂に素材変更し、コストダウンを実現しました。
STORY
「金属部品を樹脂にして高性能・低コストを実現する」
自動車メーカーは進化するテクノロジーに対応すべく、車載半導体部品の製造工程において変革を断行している。金属から樹脂への素材変更もその一つ。代表的な例が、従来のアルミニウム製からポリイミド樹脂・MCナイロンへの変換である。部品を軽量化し、機械自体の費用や稼働コストを抑え、製造効率を高める。競合同士がそのための技術を競い合っていた。 F・S・エンジニアリングに取引先の自動車部品メーカーから依頼があったのは、そんな厳しい競争の中、変化を求められていたからだった。「車載半導体の製造ラインで使用しているガイドブロックを、現状の性能は維持しつつ、コストダウンしたい…」。 そこで提案されたのが、従来のアルミニウムで作られた金属製部品を樹脂で作り変えるという挑戦的なアイデアだった。
素材変更への大きな挑戦
古くから使われてきた金属製部品を樹脂で製作するという提案に最初は戸惑いが広がった。単純に素材を変更するだけで、費用を抑えることは可能なのか。アルミのような金属ほど、樹脂は精度が出せない。図面変更などどこまで現状変更が許容されるのか。金属部品を樹脂化する場合の注意点は多くあった。だが、FSエンジニアリングの若きエンジニアは、新しい可能性に目を輝かせた。彼らは、この挑戦を受け入れ、樹脂のポテンシャルを信じて奔走することになる。
迫る納期と素材の選択
まず素材は、MCナイロンの中でも静電気のリスクに対応した帯電防止グレードを有するMC501CDR6を採用。アルミより安価な樹脂材で生産コストを抑えることを提案した。また、製造機器自体の軽量化を図りつつ、部品の耐摩耗性・摺動性を確立してスムーズな製造動作を計画した。寸法精度も実作業レベルで検証し、従来のアルミで±0.01公差としていた箇所がそこまでの精度を必要としないことを確認。±0.05に公差許容し、図面変更が行われた。
当該パーツのガイドブロックは、縫い付け用の穴2箇所の位置が近く、素材特性を考慮した加工が必要だった。MCナイロンという縮みやすい樹脂を図面寸法どおりで加工した場合、製品を実際に機械設備へ取り付けるまでに寸法変化を起こしてしまうリスクがあるからだ。公差範囲に納める寸法を明確に意識しながら、加工後に寸法変化することを計算して、あえて図面の数値を調整して切削加工する。熟練の知識と経験からなる、樹脂切削の高い技術が発揮された。
加工は自動で工具を交換する機能を有し、連続で効率よく加工を行うことができるマシニングセンタ「FANUC α-T21iEL」で行った。弊社が所有するロボドリルは、高精度な解析・制御システム・高速位置決め・形状誤差を最小限に止める高能率を備えた主軸30番の高速万能AI CNCドリルで、MC501CDR6で製作するガイドブロックの複雑な段差形状やザグリ穴加工、細かな溝加工・自由曲面をスムーズかつ的確に加工した。
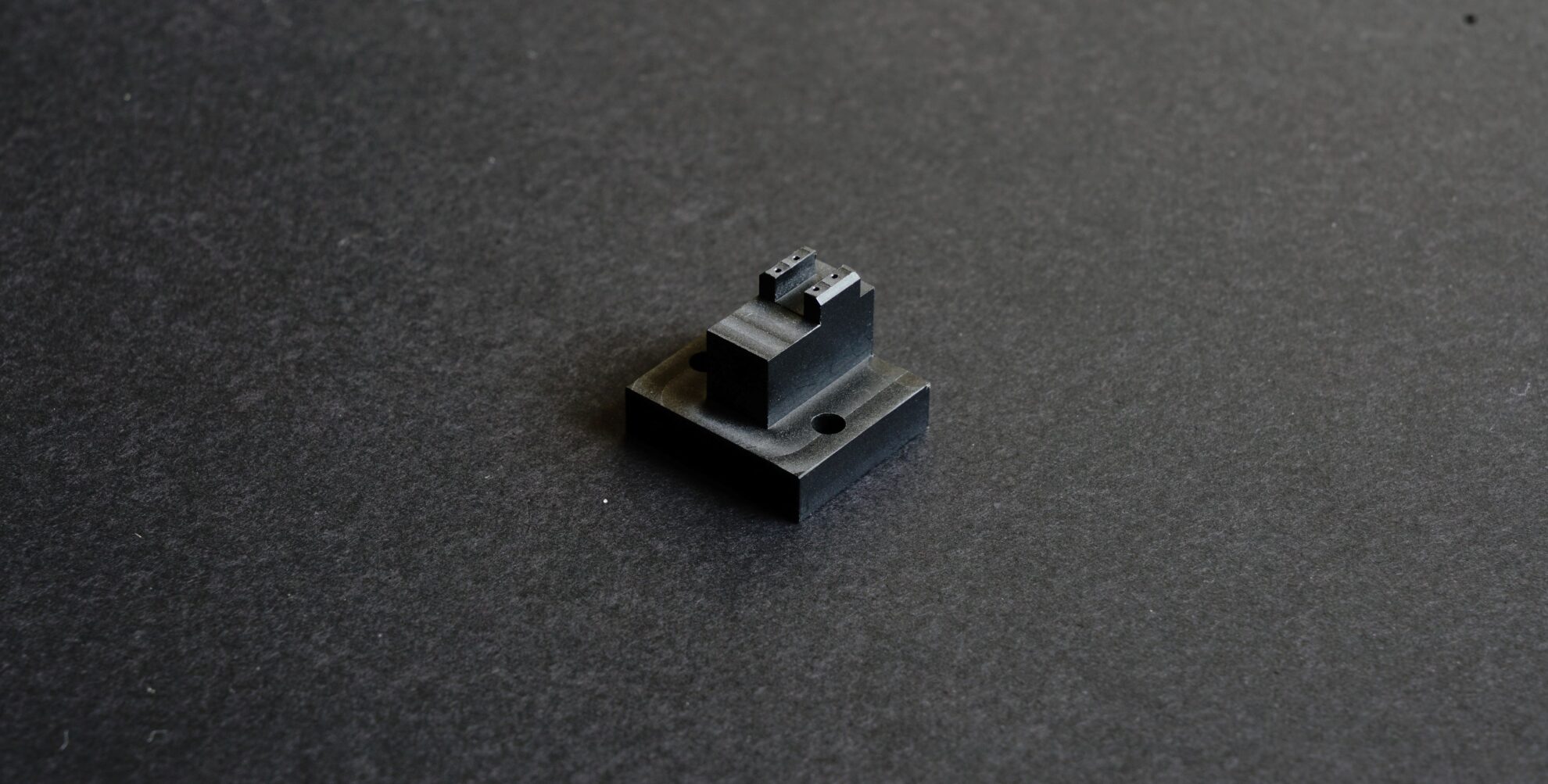
この素材変更は、コストダウンはもちろん、車載半導体の製造工程の性能向上と耐久性の向上も目指している。 ポリイミド樹脂は高い耐熱性を持ち、電気絶縁性にも優れている。これにより、半導体の高温環境での信頼性が向上し、車載エレクトロニクスの性能向上に寄与している。また、金属よりも軽量で、製造工程においても柔軟性があり、設計の自由度を高めることになった。
樹脂の軽さと柔軟性が、部品の設計・製造に機能的にも価格的にも革命をもたらすことを確信したF・S・エンジニアリング第一製造部のエンジニア達は、各部門のスタッフを巻き込んでMCナイロンの切削加工法について研究と試作に取り組んだ。そして、MC501CDR6の特性を理解し、加工技術を検討する中で、金属にはない軽さや耐久性、そしてコストダウンを引き出す方法をついに見つけ出したのだった。
性能を維持しつつコスト削減
結果的にこのプロジェクトは約10%のコストダウンに成功しつつ、製造ラインの性能は従来の水準を維持するという目標も達成した。この事例は、車両の先進運転支援システムや自動運転技術の進化においても、製造工程の改善策の一つとして注目され、エネルギー効率の向上や車両の信頼性向上にも寄与している。車載半導体部品の樹脂転換は、自動車産業において技術的な進化を促進し、未来のモビリティを切り拓いている。
困難な道のりを歩みながらも“高性能・低コスト”という確かな成功を掴み取り、樹脂のポテンシャルがもたらす未知の可能性にあらためて期待感が高まった。
安価で安定供給できる樹脂パーツであれば、コストダウンが現実になる。
金属部品を樹脂に変更することで、約60%程度の軽量化が実現できる。
軽量化が達成できれば、機械設備に必要な電力などの稼働エネルギーを削減できる。
樹脂の特性を理解し、適材適所のアプローチができれば、金属に代わりエンジニアプラスチックが製造工程の主軸になるのだ。
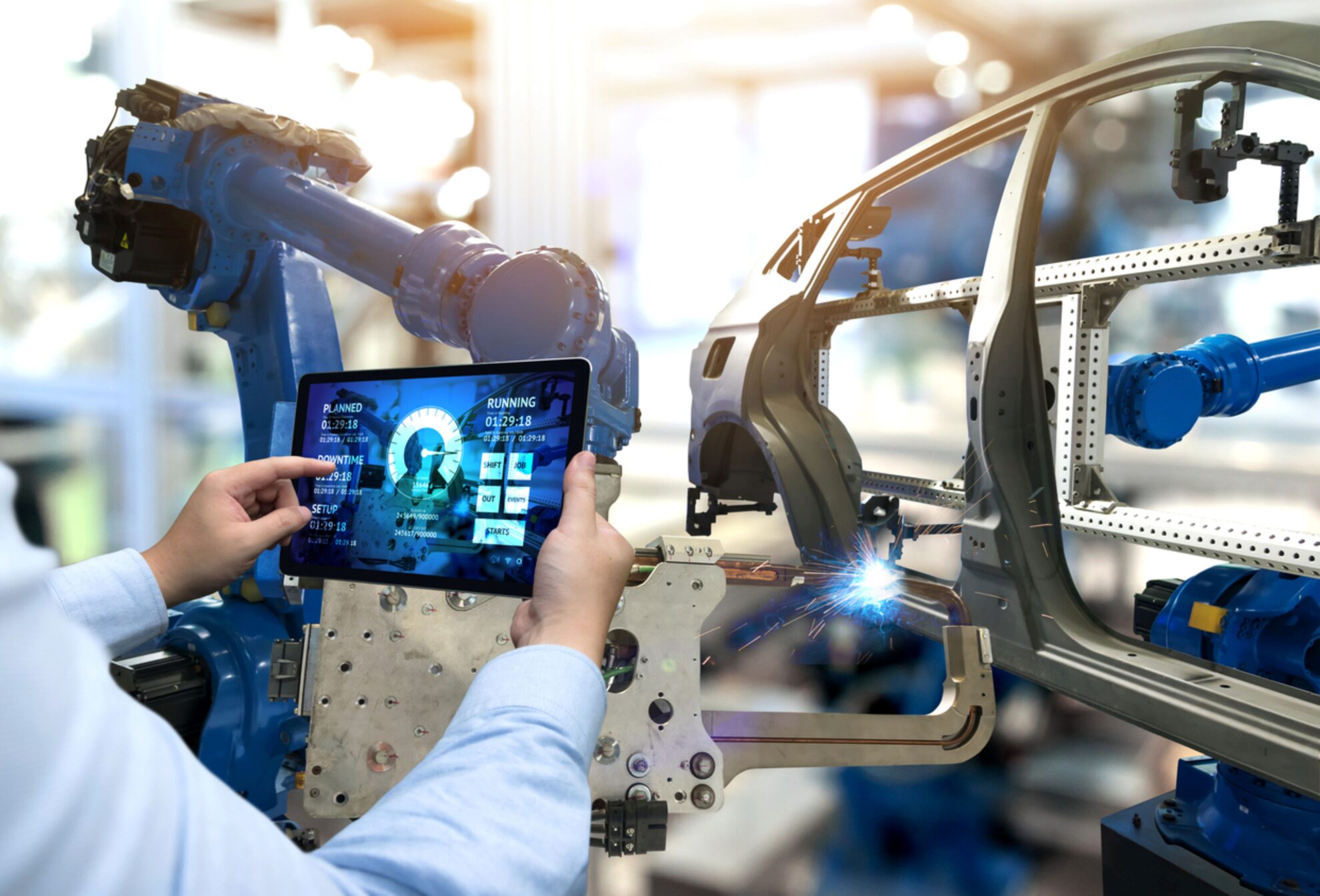
試行錯誤が続いたが、エンジニア達は「樹脂パーツ主体の効率的な製造現場」を信じて立ち上がり、新しい部品を成功裏に完成させた。
それは、F・S・エンジニアリングが樹脂の可能性を広げる冒険に、大きな一歩を踏み出した瞬間だった。
樹脂切削品の一例
たとえばこのようなパーツを製造致しました。
精密機器 装置内治具
- 精密機器の製造装置 樹脂パーツ
- PEEK
- L 31mm
POINT
- 製品の破損や傷の発生を防ぐため、金属から樹脂に素材変更。
- 樹脂素材は、優秀な機械的強度を誇る高性能プラスチックであるPEEK。
- 複合旋盤にて、先端のプラス形状および横穴を効率的に加工。
食品加工 異物検査機 シャフト
- コンベア装置の回転軸部分
- POM
- 408mm×φ45mm
POINT
- スムーズに製品を流すため、ベルトへ均等にテンションをかけるように設計。
- クラウン形状(中央と両端で寸法差異がある)で加工することで、一定のテンションを保つ。
- 素材は、金属より軽量・静か・錆びないという利点のある樹脂材・POM。